-
Shaping the future of supply chain
-
4flow Trendmonitor
-
Supply Chain Orchestration
-
Referenzprojekt Thalia
-
Ausgewählte Success Stories
EntdeckenDiese Kunden vertrauen uns
Als innovativer Partner entwickeln wir gemeinsam mit unseren Kunden Lösungen für die Zukunft.
Jetzt kontaktieren
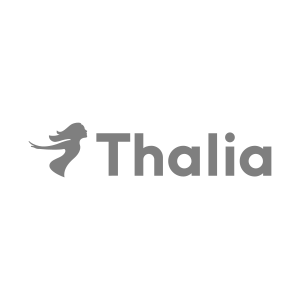
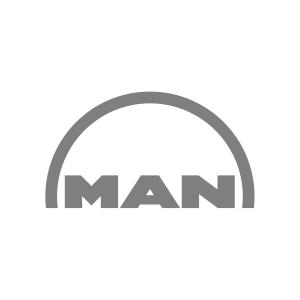
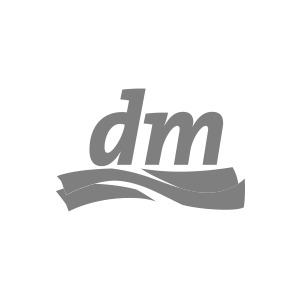
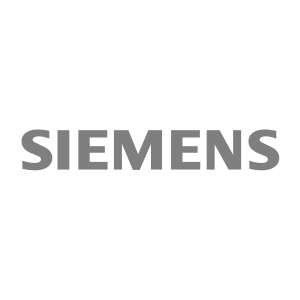
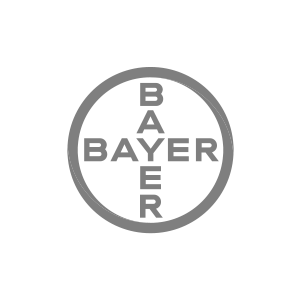
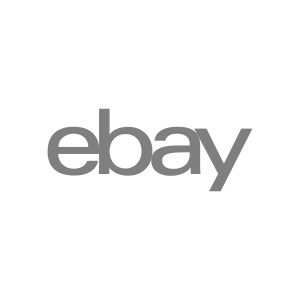
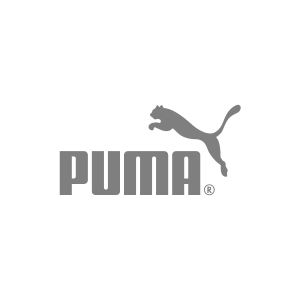
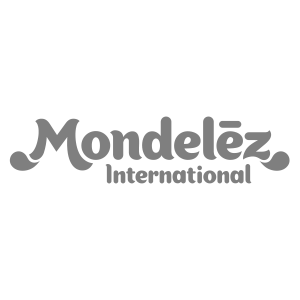
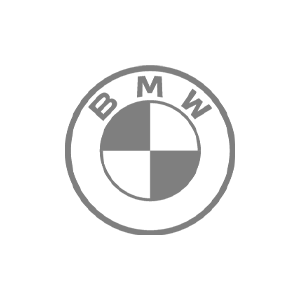
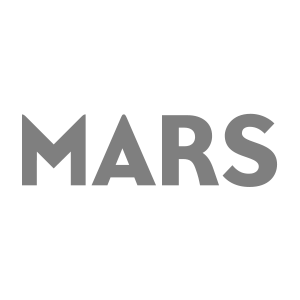
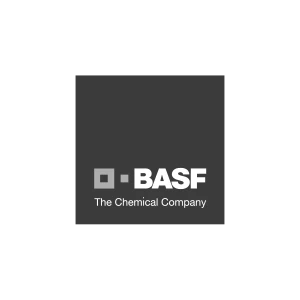
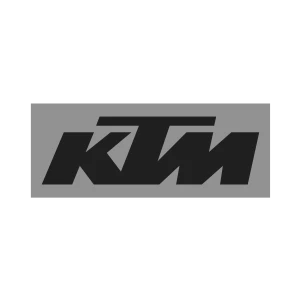
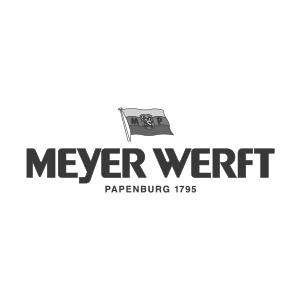
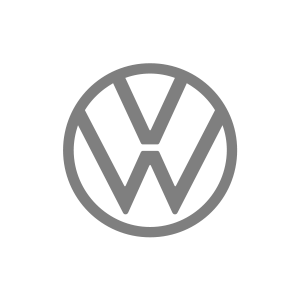
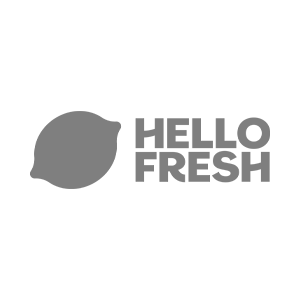
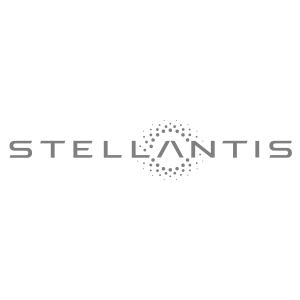
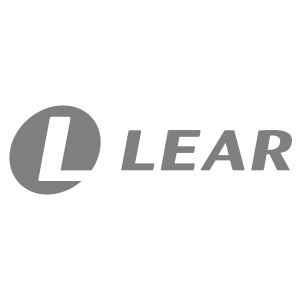
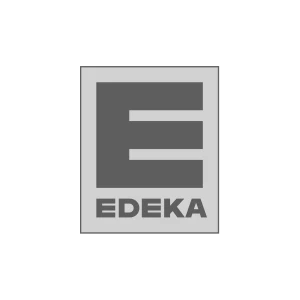
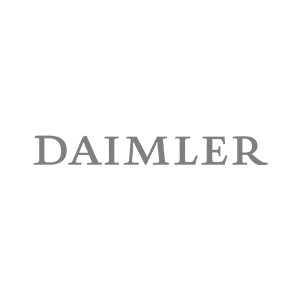
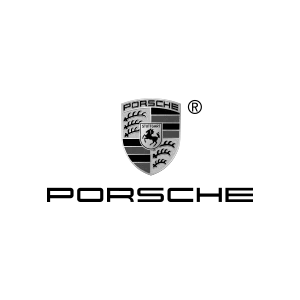
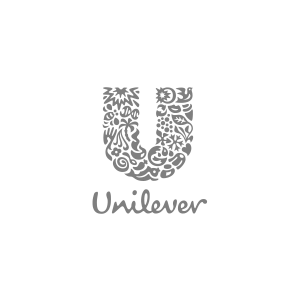
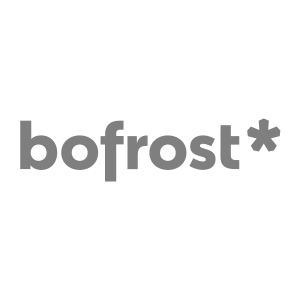
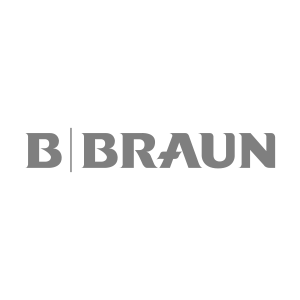
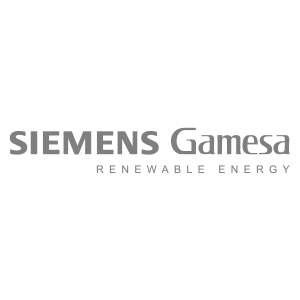
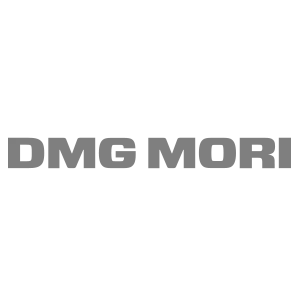
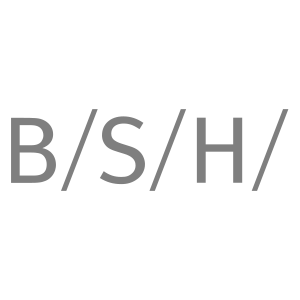
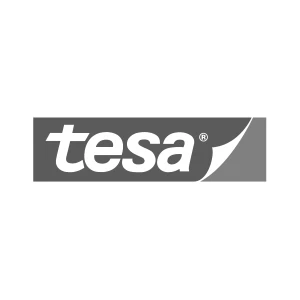
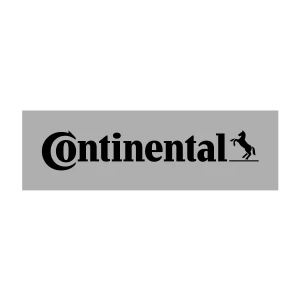
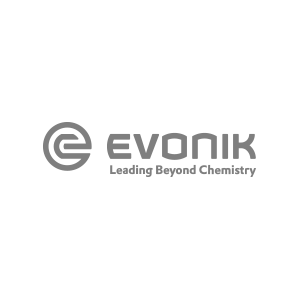
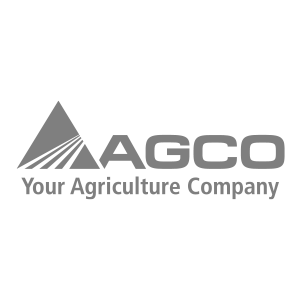
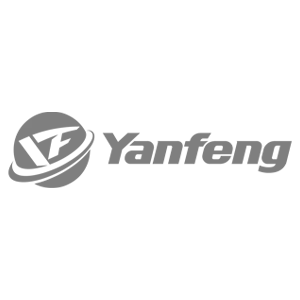
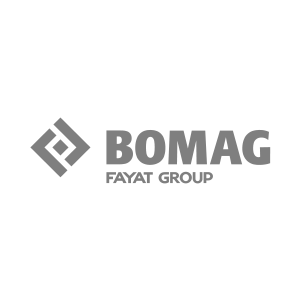
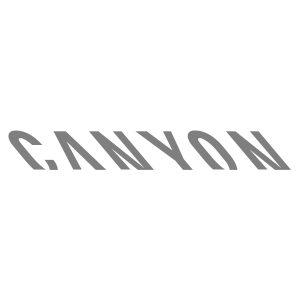
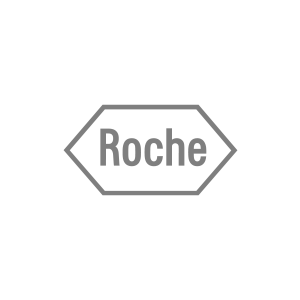
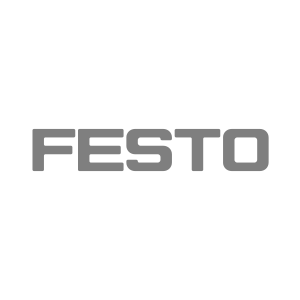
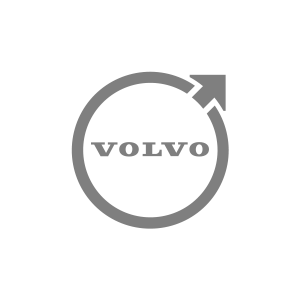
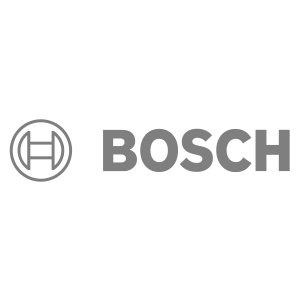
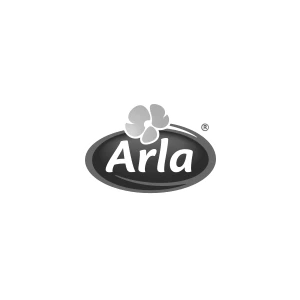
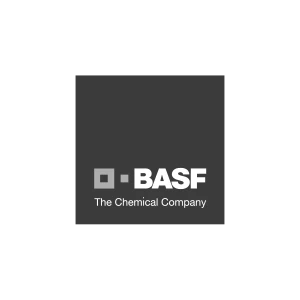
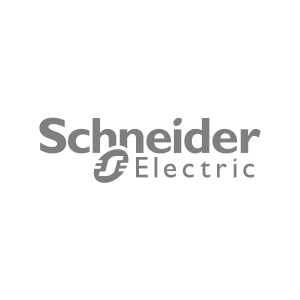
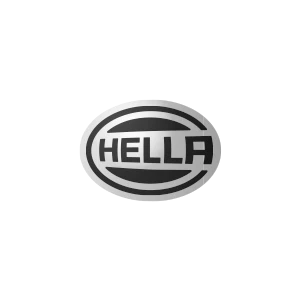
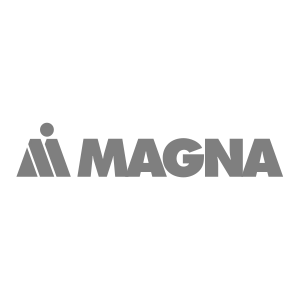
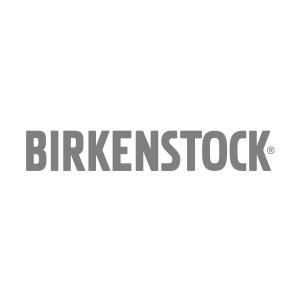
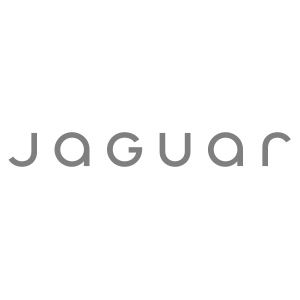
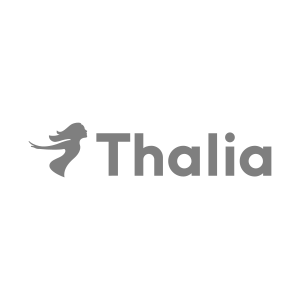
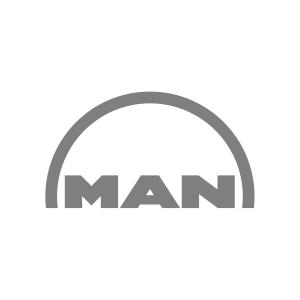
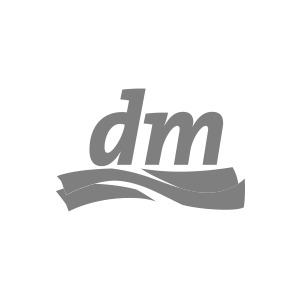
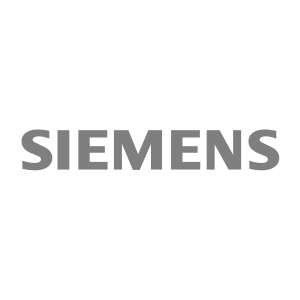
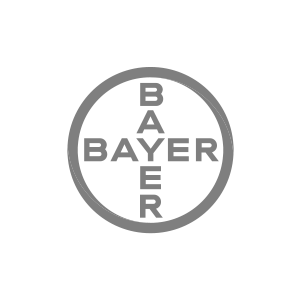
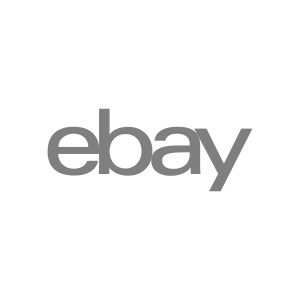
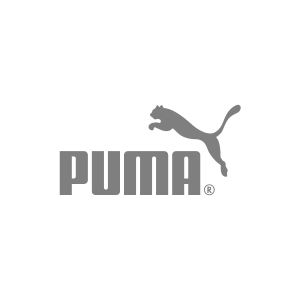
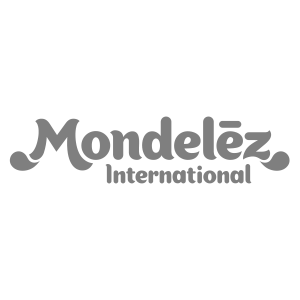
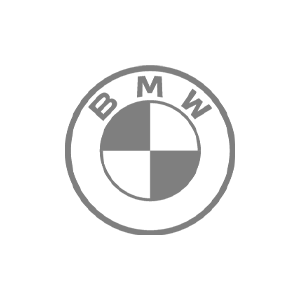
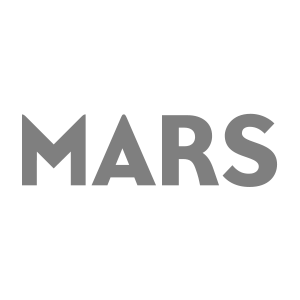
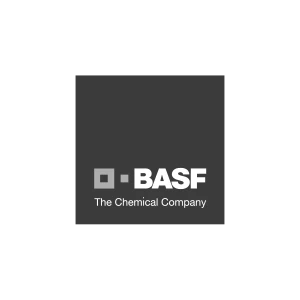
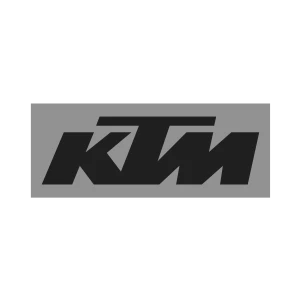
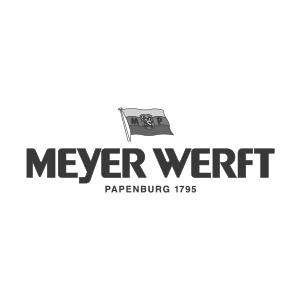
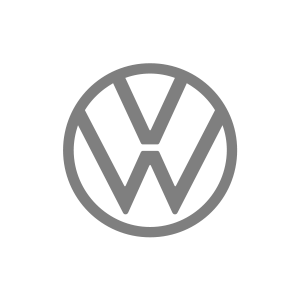
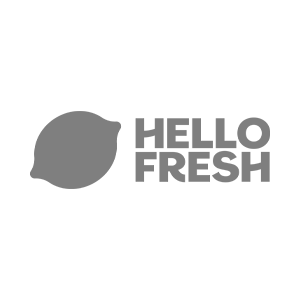
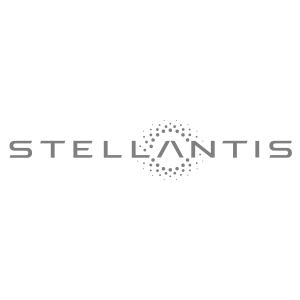
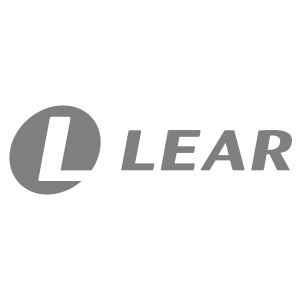
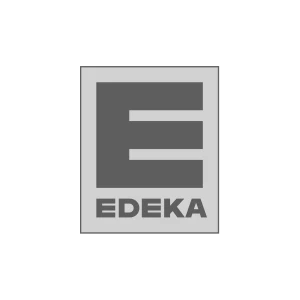
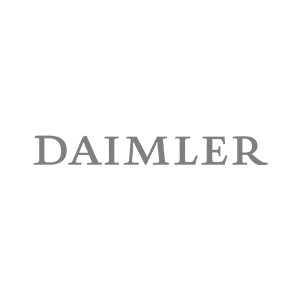
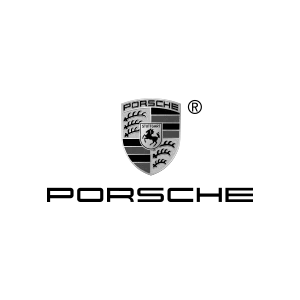
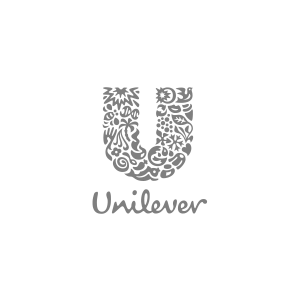
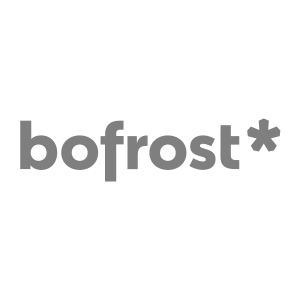
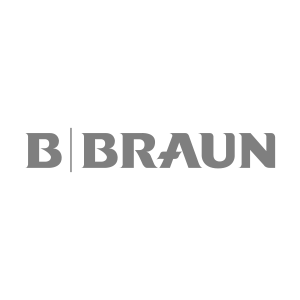
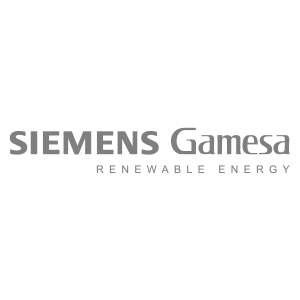
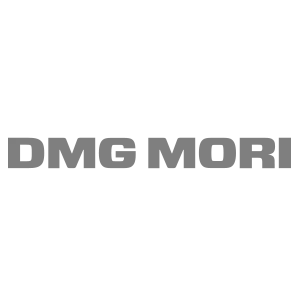
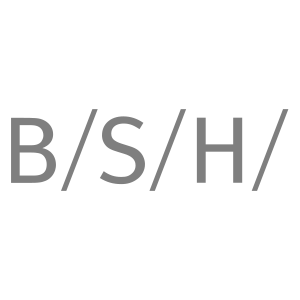
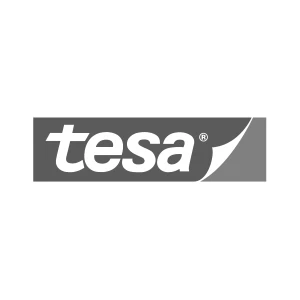
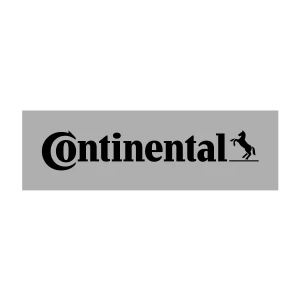
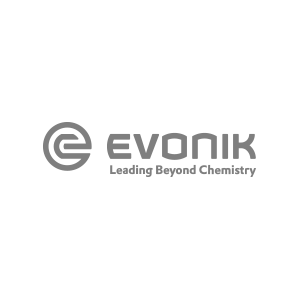
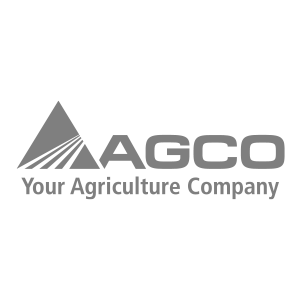
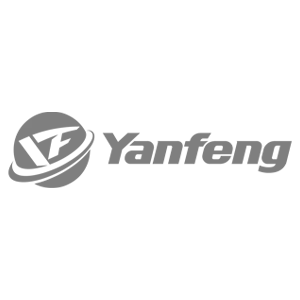
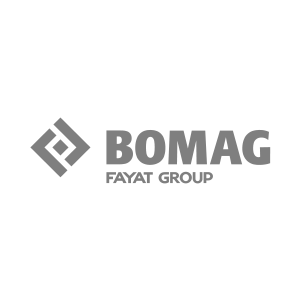
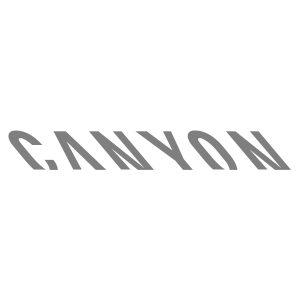
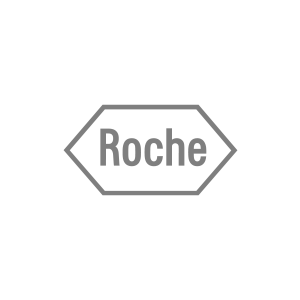
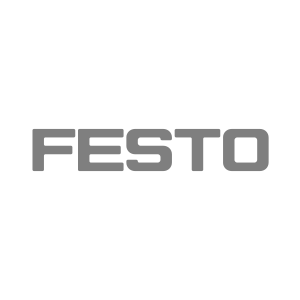
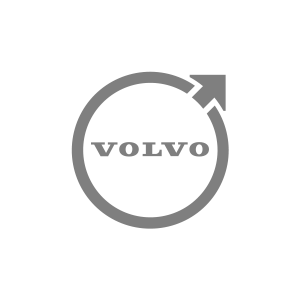
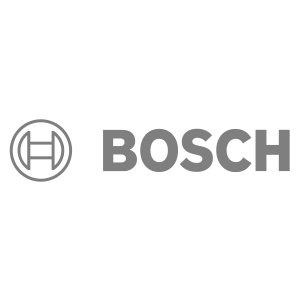
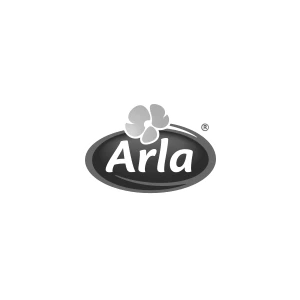
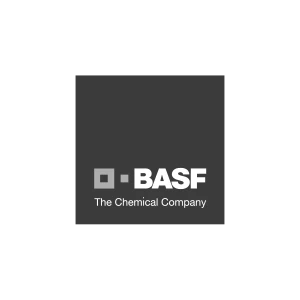
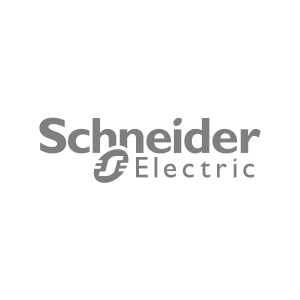
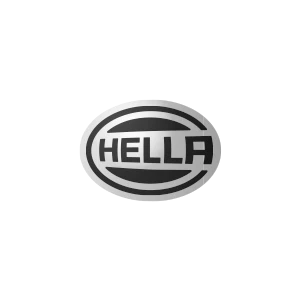
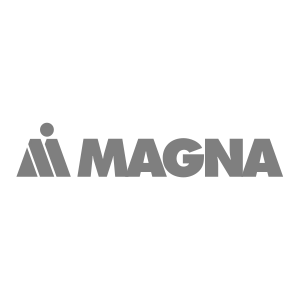
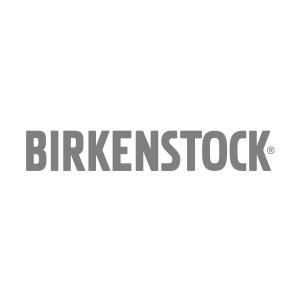
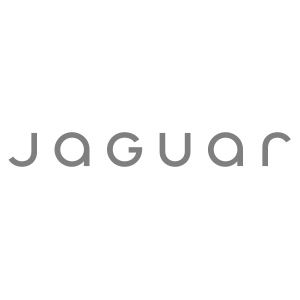
20+ Standorte weltweit
4flow wächst seit der Gründung im Jahr 2000 kontinuierlich und erfolgreich. Mit Standorten in Nord- und Südamerika, Europa und China sind wir für unsere internationalen Kunden global präsent und arbeiten sehr kundennah.
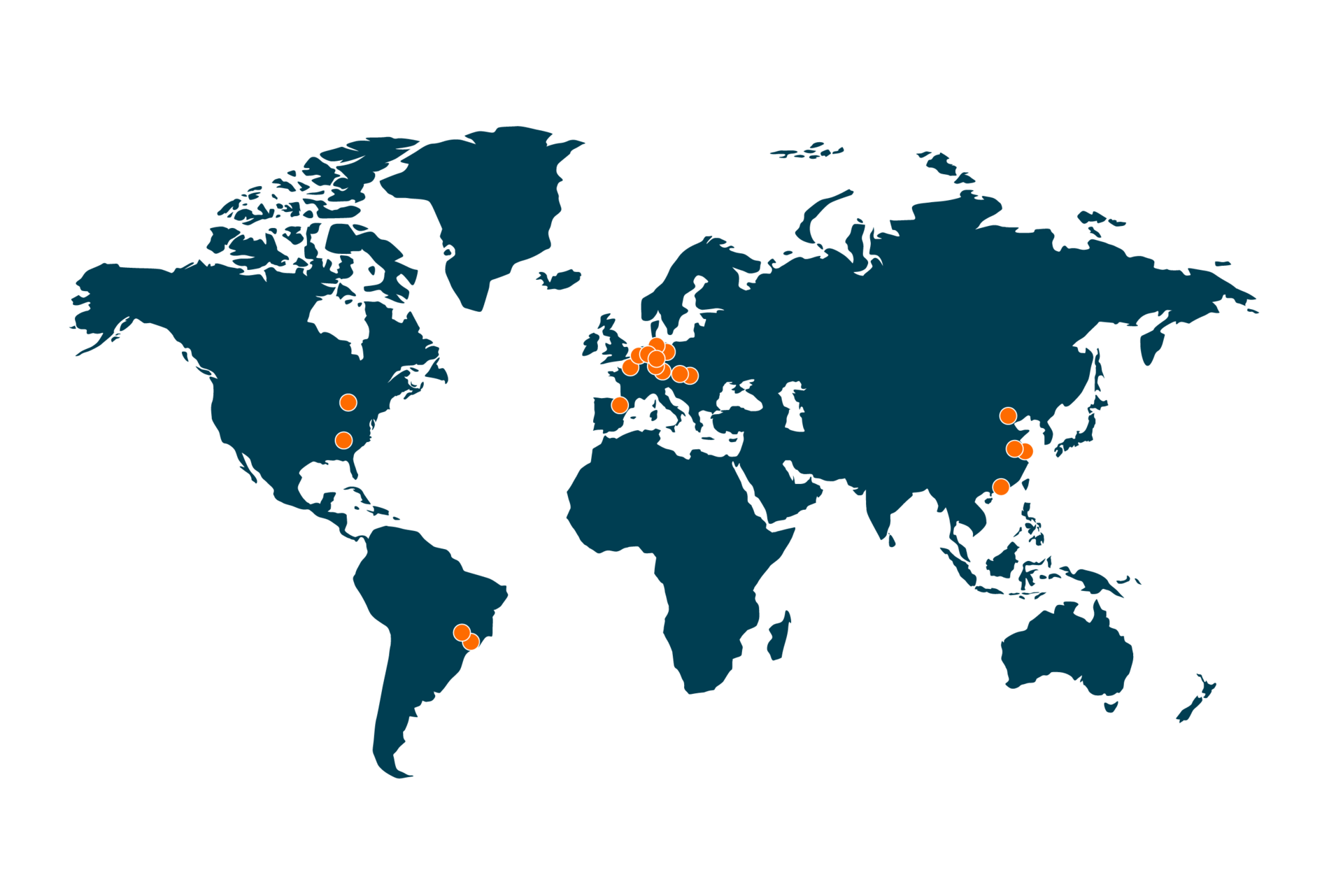
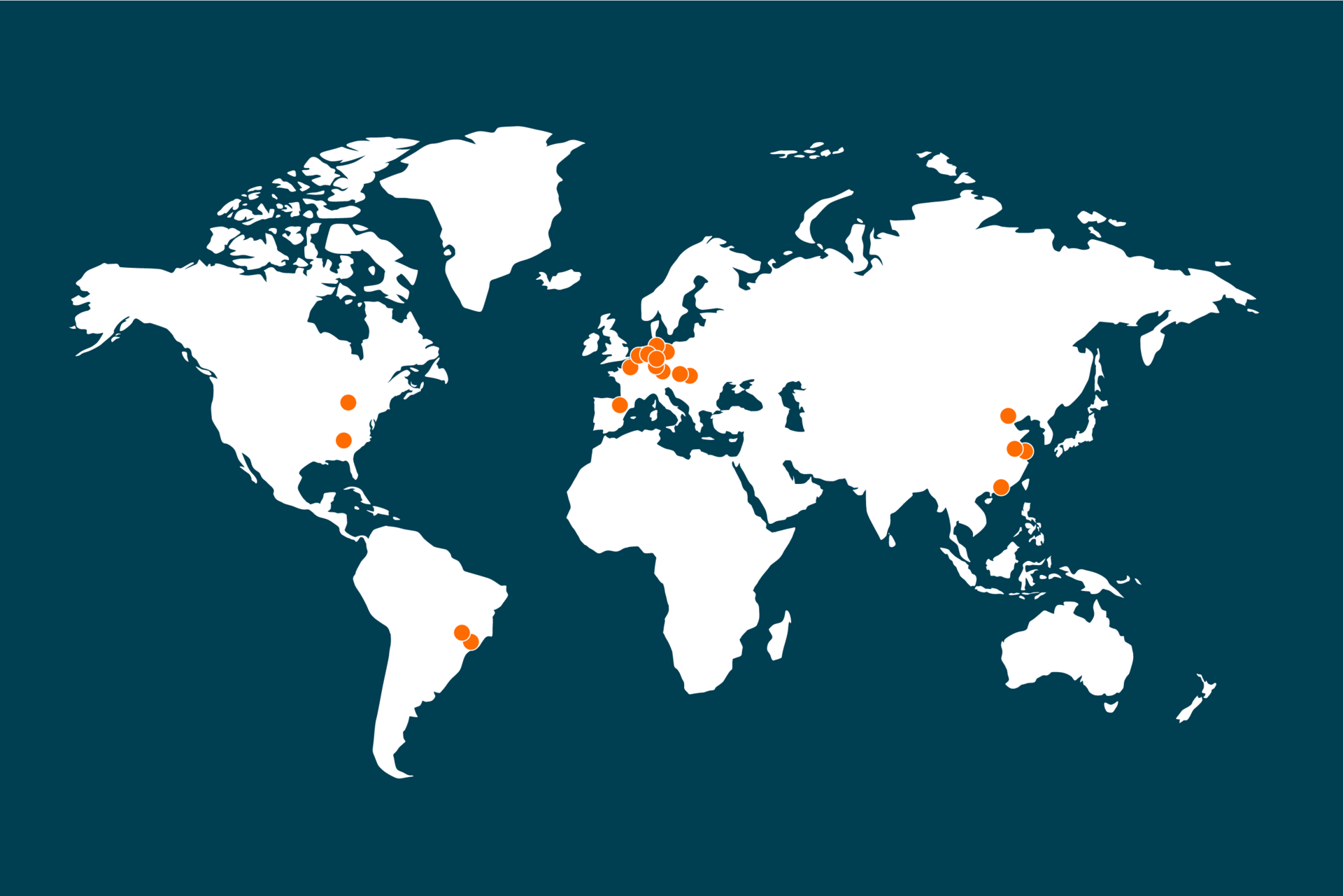
Events
Anstehende Events
Webinare on demand
Webinare on demand
What´s new?
EntdeckenBereit, Ihre Supply Chain zu optimieren?
Als innovativer Partner entwickeln wir gemeinsam mit unseren Kunden Lösungen für die Zukunft.